The Power of Predictive Maintenance: Transforming Asset Management
In today's highly competitive business landscape, organizations continuously seek ways to optimize performance and minimize downtime. Maintenance can be broadly categorized into four main types, each with its unique approach to ensuring equipment efficiency and longevity. These include reactive maintenance, preventive maintenance, predictive maintenance (PdM), and condition-based maintenance. Reactive maintenance, also known as "run-to-failure" maintenance, involves repairing or replacing equipment only after it has failed. While this approach may have lower initial costs, it can lead to higher downtime and unexpected expenses. On the other hand, preventive maintenance involves performing scheduled maintenance tasks regardless of equipment condition, which can lead to unnecessary work and inefficient use of resources. Predictive maintenance utilizes data, analytics, and IoT technology to anticipate equipment failure, allowing organizations to schedule maintenance activities before a breakdown occurs. Lastly, condition-based maintenance involves monitoring equipment in real-time and performing maintenance tasks only when specific conditions are met, which can optimize resource allocation and reduce downtime. Within this post, we will focus on predictive maintenance.
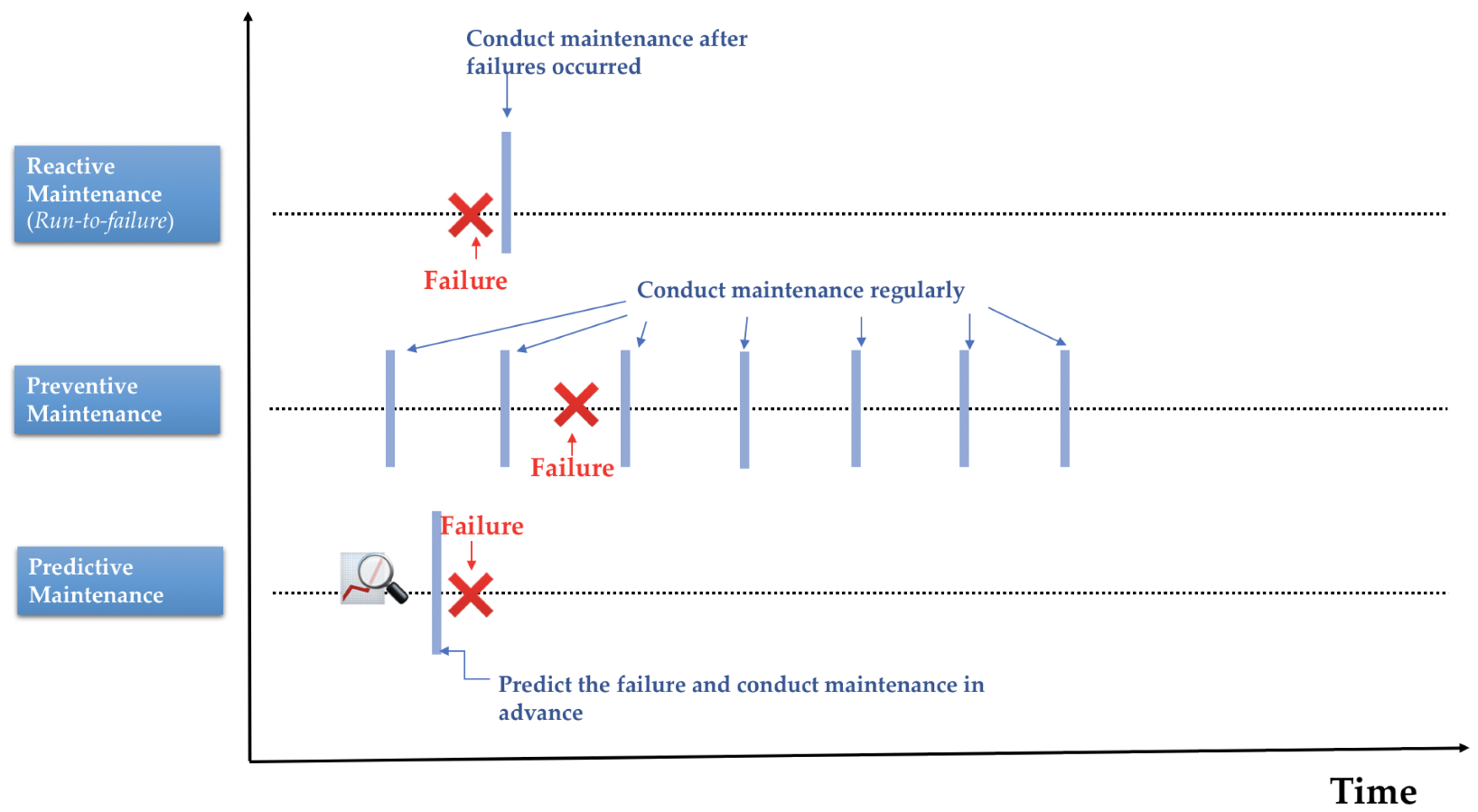
Predictive maintenance has emerged as a game-changer, transforming how businesses manage their assets. Gartner has estimated that by 2022, global spending on IoT-based predictive maintenance will rise to around $13 billion. It was also estimated that IoT-enabled predictive maintenance monitoring assets would lead to massive savings of around 40% for businesses using the technology. PdM is a proactive approach to asset management that leverages data, analytics, and IoT technology to predict when equipment is likely to fail, allowing organizations to schedule maintenance before a breakdown occurs. Unlike reactive maintenance, which addresses issues after they arise, or preventive maintenance, which relies on predetermined schedules, It focuses on data-driven insights to optimize maintenance activities and prevent unplanned downtime.
Predictive maintenance can be used to improve asset reliability by identifying potential issues early, reducing maintenance costs, extending assets' lifetime, and increasing safety in the facility. Predictive maintenance's power lies in combining several key technologies like sensors and IoT devices, communication, data analytics, visualization and dashboards.
Predictive maintenance has been used across various industries, including:
- Manufacturing: To reduce downtime and maintain smooth operations, factories utilize PdM to monitor the condition of vital production machineries like motors and pumps.
- Energy & Utilities: To prevent outages and guarantee a consistent power supply, power plants and utility companies utilize PdM to forecast the breakdown of transformers, turbines, and other crucial infrastructure.
-
Transportation: To reduce downtime and increase efficiency, fleet operators and airlines utilize PdM to proactively schedule maintenance and repairs while monitoring the condition of their vehicles and aircraft.
- Healthcare: To ensure that life-saving devices like ventilators and MRI machines remain functional and lower the chance of unforeseen failures, hospitals and medical facilities employ PdM to monitor the functioning of these devices.
In conclusion, predictive maintenance has emerged as a powerful tool for modern businesses, helping them optimize asset management, reduce costs, and improve operational efficiency. By harnessing the power of data, analytics, and IoT technology, companies can unlock the full potential of their assets and gain a competitive edge in their respective industries.
References:
[1] Arena, F., Collotta, M., Luca, L., Ruggieri, M., & Termine, F. G. (2022). Predictive maintenance in the automotive sector: A literature review. Mathematical and Computational Applications, 27(1), 2.
buy @buy2cbonline.com apvp 3cmc 4mmc coke 2cb powder in usa eu
Buy2cbonline.com - @Buy2cbonline.com/shop/ | your #1 source for top quality premium RC's research chemicals like 2cb powder 2fdck (2-FDCK) 3cmc crystal meth 4mmc eutylone mephedrone ketamine Ephedrine hcl powder A-pvp etizolam bromazolam alprazolam powder Mdphp freebase Coke and more .
Buy Crystal Meth online | Order Crystal Meth online | Crystal Meth price per gram Canada USA AUS | Buy Cheap Crystal Meth online AUS Canada USA Europe, can I buy crystal meth online?
https://buy2cbonline.com/product/buy-crystal-meth-online/
Buy Mdphp Freebase online | Order Mdphp Freebase online Monkey Dust Mdphp freebase for sale https://buy2cbonline.com/product/order-monkey-dust-online-mdphp/
Buy Ketamine online | Order Ketamine online Australia | ketamine Price per gram https://buy2cbonline.com/product/buy-ketamine-online/
Buy 5f-mdmb-2201 online - https://buy2cbonline.com/product/5f-mdmb-2201-for-sale-online/
Buy JWH-018 online | Order JWH-018 online | JWH-018 Price per gram - https://buy2cbonline.com/product/buy-jwh-018-online/
Buy Cocaine online AUS | Order Cocaine online Australia | Cocaine price per gram Australia
https://buy2cbonline.com/product/buy-fish-scale-cocaine-online-fast/
Do you want to buy 2FDCK online? 2-fdck for sale 2fdck buy usa canada Australia uk | 2fdck for sale Buy 2fdck online | Order 2fdck online AUS canada UK | 2fdck price per gram 2fdck for sale | buy 2fdck usa buy 2fdck usa https://buy2cbonline.com/product/2-fdck-for-sale/
Buy Ephedrine hcl online | Order Ephedrine hcl online AUS Ephedrine hcl price per gram AUS
https://buy2cbonline.com/product/buy-ephedrine-online-hcl-powder/
Buy Alpha-pvp online | Order Apvp online | Apvp Price per gram AUS canada USA | Apvp price per kg in Australia https://buy2cbonline.com/product/buy-a-pvp-online-usa/
Buy Clonazolam online - https://buy2cbonline.com/product/buy-clonazolam-powder-online/
Buy 2C-I powder online - https://buy2cbonline.com/product/2c-i-powder-for-sale-online-safely/
Buy Bromazolam powder online | Order Bromazolam online AUS | Bromazolam Price per gram https://buy2cbonline.com/product/buy-bromazolam-powder-online/
Buy 2CB powder online | Order 2CB powder online | 2CB price per gram Australia canada USA Europe- https://buy2cbonline.com/product/buy-2cb-powder-online/
Buy Mephedrone online | Buy 4mmc online | Buy 4mmc Mephedrone Meow online | 4mmc Mephedrone price per gram | Where to buy Mephedrone 4mmc online ?
https://buy2cbonline.com/product/buy-mephedrone-online-4mmc/
Buy Alprazolam powder online Order Alprazolam Powder Online | Alprazolam Powder Price per gram in Australia Buy Cheap Alprazolam Powder Online https://buy2cbonline.com/product/alprazolam-powder/
Buy protonitazene online | Order Protonitazene Online https://buy2cbonline.com/product/hydrochloride-protonitazene-for-sale/
Buy 3CMC crystal online Order 3CMC online | 3CMC price per gram |Buy Cheap 3CMC online| https://buy2cbonline.com/product/buy-3cmc-crystal-3-cmc-online/
Order eutylone online , eutylone crystal for sale, best price eutylone, eutylone supplier, order eutylone Europe, buy eutylone online eu uae usa
https://buy2cbonline.com/product/eutylone-eutylone-crystal/
Buy 5cladba 5cl online | Order 5cladba 5cl Online in Australia - https://buy2cbonline.com/product/buy-5cladba-safely-online/
Buy Alprazolam Powder Online|Order Alprazolam Powder Online | Alprazolam Powder price per kg Apvp @buy2cbonline.com
Threema: 3F3YDZMD
Telegram: @DHlabo
https://t.me/MdphpFreebaseEurope
WhatsApp: +44 7507412275